A 115-year-old success story!
REP international : A World Leader in Rubber Machinery
The REP company has been selling injection molding machines since 1948. Very early on, REP understood the importance of polymers and elastomers to industry and decided to specialize in the rubber injection technology.
Key Events and Dates of REP's History
Our advantages ?
"Exclusive solutions and an international network of sales and aftersales agents"
Our core know-how?
"A high-technology range of vertical and horizontal rubber injection molding machines"
Our motto
"Rubber in Motion"
Our philosophy
"Using new ideas to achieve sustainable productivity"
... and before that?
Founded in 1907 by Robert Esnautlt Pelterie, an aviation pioneer and a major theorist in the field of astronautics, the initials REP were first used as a plane logogram until the company turned to the metal industry.
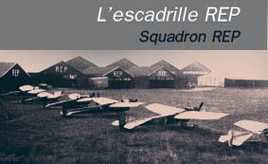
Want to learn more?
Read the book "Robert Esnault-Pelterie, du ciel aux étoiles, le génie solitaire" (From sky to the stars, a solitary genius) by Félix Torres and Jacques Villain (Publisher: Confluences Editions)